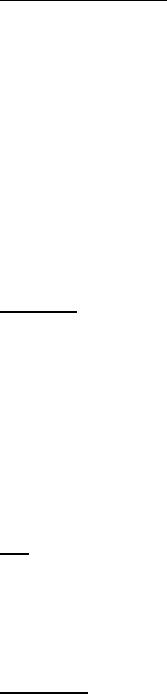
MIL-HDBK-1390
components. This reliability block diagram is the first gross breakout of candidate items requiring LORA. The
system level reliability requirement is then allocated down the reliability block diagram in a top-down approach and
is levied on the equipment designers. LORA, at this point, can be used as a design tool for conducting tradeoff
analyses to determine whether to design an item for repair or discard. Reliability predictions are applied in a
bottoms-up approach as the design progresses to determine whether the reliability allocations are feasible and
attainable. Thus, LORA, which uses the failure rates determined in reliability prediction, becomes more accurate
and detailed. In conducting LORA, the FMECA is used to provide a candidate list of items that are critical to
reliability and will affect readiness. The LORA analyzes the reliability critical items to determine whether they are
maintenance significant.
4.2.2.3 Maintainability engineering. Maintainability engineering is the process of designing the materiel
system such that it can be maintained with accuracy, economy, and ease. The maintainability program involves
several tasks which are used to define, develop, and improve the maintainability of a system. With respect to
LORA, the maintainability engineering process, to a large extent, tracks with the reliability engineering process.
Many of the activities pertaining to maintainability engineering relate to LORA (i.e., maintainability modeling,
maintainability allocations, maintainability predictions, Failure Modes and Effects Analysis (FMEA), and
maintainability analysis). The maintainability model is typically consistent with the reliability model described
above and is used as a tool to perform allocations and predictions. The maintainability allocation and prediction
tasks have the same functions as the reliability allocation and prediction tasks. However, in maintainability
engineering, terms such as Mean Time To Repair (MTTR), not failure rates, are being allocated or predicted. The
FMEA is consistent with the FMECA, except that the FMEA is used to ascertain information which relates to fault
detection and isolation that are critical drivers of maintainability at all levels of maintenance. Unlike the FMECA,
the FMEA does not assess the severity of a failure's consequence. The maintainability analysis task translates data
into a detailed maintainability design approach to achieve the system MTTR requirements. LORA plays a vital role
in maintainability analysis in that it evaluates the maintainability design alternatives. Also, LORA uses the MTTR
data as input for evaluating repair level or discard decisions to meet the overall subsystem and component
availabilities and constraints.
4.2.2.4 Provisioning. Provisioning is the process of determining and acquiring the range and quantity of
spares and repair parts and support and test equipment required to operate and maintain an end item of materiel for a
period of service throughout the life cycle to include initial fielding, Engineering Change Proposals (ECP),
obsolescence, and other support and sustainment efforts. Provisioning involves several tasks (e.g., cataloging, SMR
coding, assignment of failure factors, maintenance replacement rates, consumption expenditures, essentiality coding,
identification of maintenance significant items, determination of Maintenance Task Distributions (MTD),
Replacement Task Distributions (RTD)) and interfaces with various other efforts (e.g., maintenance planning, MAC
development, LORA, RAM analyses, FMECA) to ensure the timely availability of minimum initial stocks of
support items at the least initial investment cost the system readiness can achieve. It should be noted the
development of failure factors involves the manipulation of failure rates derived in reliability engineering. LORA,
relative to provisioning and optimization, provides the analytical basis from which the maintenance portion of the
SMR code is obtained and identifies maintenance significant items. In addition, LORA is the analytical basis for the
development of a MAC. The MAC and SMR code are then used to determine MTD and RTD.
4.2.2.5 LPD. The LPD, described in SAE GEIA-STD-0007, provides a structured method to record support
requirements data from PSA tasks, such as LORA. Also, other analyses are documented in the LPD, such as
FMECA, RCM, and Reliability, Availability, and Maintainability (RAM). The LORA can use data from the LPD as
other analyses are completed and documented (i.e., Mean Time Between Failure (MTBF), MTTR, unit price,
deployment/usage). The LPD provides a common consistency of data among the various analyses being conducted
and a vital source of updated information as the weapon system under acquisition matures through the life cycle
phases.
4.2.3 End user input. The end user can provide valuable insight into problem areas associated with various
maintenance support concepts. The LORA process should incorporate end user input by assessing field-generated
maintenance data and materiel readiness monitoring systems. Evaluating the adequacy of existing maintenance
concepts and involving end user stakeholders at critical decision points in the LORA process will assist in achieving
an effective and efficient LORA program.
6
For Parts Inquires call Parts Hangar, Inc (727) 493-0744
© Copyright 2015 Integrated Publishing, Inc.
A Service Disabled Veteran Owned Small Business