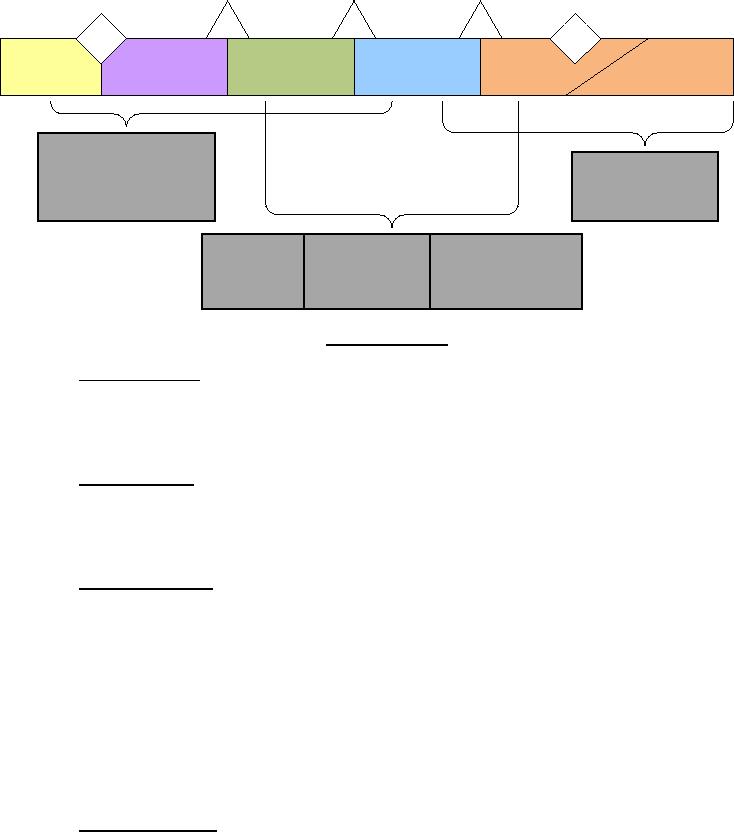
MIL-HDBK-1390
tools, and the program milestones are properly addressed and identified to prevent overlap, duplication, omission, or
schedule delays.
A
B
C
FRP
MDD
DR
Engineering &
Pre Materiel
Technology Maturation
Materiel Solution
Manufacturing
Production &
Development
Operations &
& Risk Reduction
Analysis
Support
Decision
Development
Deployment
Use conceptual data to perform
tradeoff analyses for:
Update LORAs as required:
- Number of sites
- Using operating data
- Number of items
- For ECPs
- Types of support equipment
- For SMR code changes
- MTBF break points
Outputs used as inputs to:
Perform LORAs
Use updated data from:
- Maintenance planning
- Economic
- PSA
- SMR codes
- Noneconomic
- Test and evaluation
- Provisioning
- Repair vs. discard
- Prototype
- Support equipment selection
FIGURE 1. Life cycle of LORA
4.2.1 LORA environment. The LORA environment is one that integrates design, operations, and logistic
support characteristics/constraints to establish the maintenance level at which an item will be removed, replaced,
repaired, or discarded. The establishment of LORA into the environments of systems engineering and PSA
disciplines is best seen in the regulations which require LORA, or allude to a LORA requirement, within the various
military services.
4.2.2 Interface with PSA. PSA serves as the interfacing mechanism between systems engineering and the
IPS activities. LORA, as an integral part of the PSA program, interfaces with such activities as maintenance
planning, design engineering, reliability engineering, maintainability engineering, provisioning, support equipment
development, Source Maintenance and Recoverability (SMR) coding, technical manual development, Maintenance
Allocation Chart (MAC) development, and the LPD.
4.2.2.1 Maintenance planning. Maintenance planning is the process conducted to evolve and establish
maintenance concepts and requirements for a materiel system. This process involves several analyses and programs
in addition to LORA (i.e., PSA; Reliability Centered Maintenance (RCM); Failure Mode, Effects, and Criticality
Analysis (FMECA); reliability program; maintainability program; testability). The relationship of these analyses,
for purposes of maintenance planning, are generally as follows: the FMECA (SAE TA-STD-0017, Activity 9.5)
identifies potential design weaknesses through systematic documented consideration of all likely ways in which a
component or equipment can fail, the causes for each failure mode, and the effects of each failure; RCM (SAE TA-
STD-0017, Activity 9.7) identifies preventive or scheduled maintenance tasks for an equipment end item in
accordance with a specified set of procedures and establishes intervals between maintenance tasks; task analysis
(SAE TA-STD-0017, Activity 12), analyzes required operations and maintenance tasks for the new
system/equipment; reliability program identifies the frequency of failures; maintainability program identifies the
elapsed time to correct a failure; and LORA identifies the recommended maintenance levels and support costs
associated with unscheduled maintenance tasks.
4.2.2.2 Reliability engineering. Reliability engineering is the set of design, development, and manufacturing
tasks by which reliability is achieved. Reliability engineering is comprised of several activities focusing on the
prevention, detection, and correction of reliability design deficiencies of weak parts and workmanship defects.
Several of the activities involved with reliability engineering relate to LORA (i.e., reliability modeling, reliability
allocations, reliability predictions, and FMECA). Reliability modeling reorients the functional (schematic) block
diagrams into a series-parallel network showing reliability relationships among the various subsystems and
5
For Parts Inquires call Parts Hangar, Inc (727) 493-0744
© Copyright 2015 Integrated Publishing, Inc.
A Service Disabled Veteran Owned Small Business